Mitigating Risks in MEP Engineering Through Effective Planning
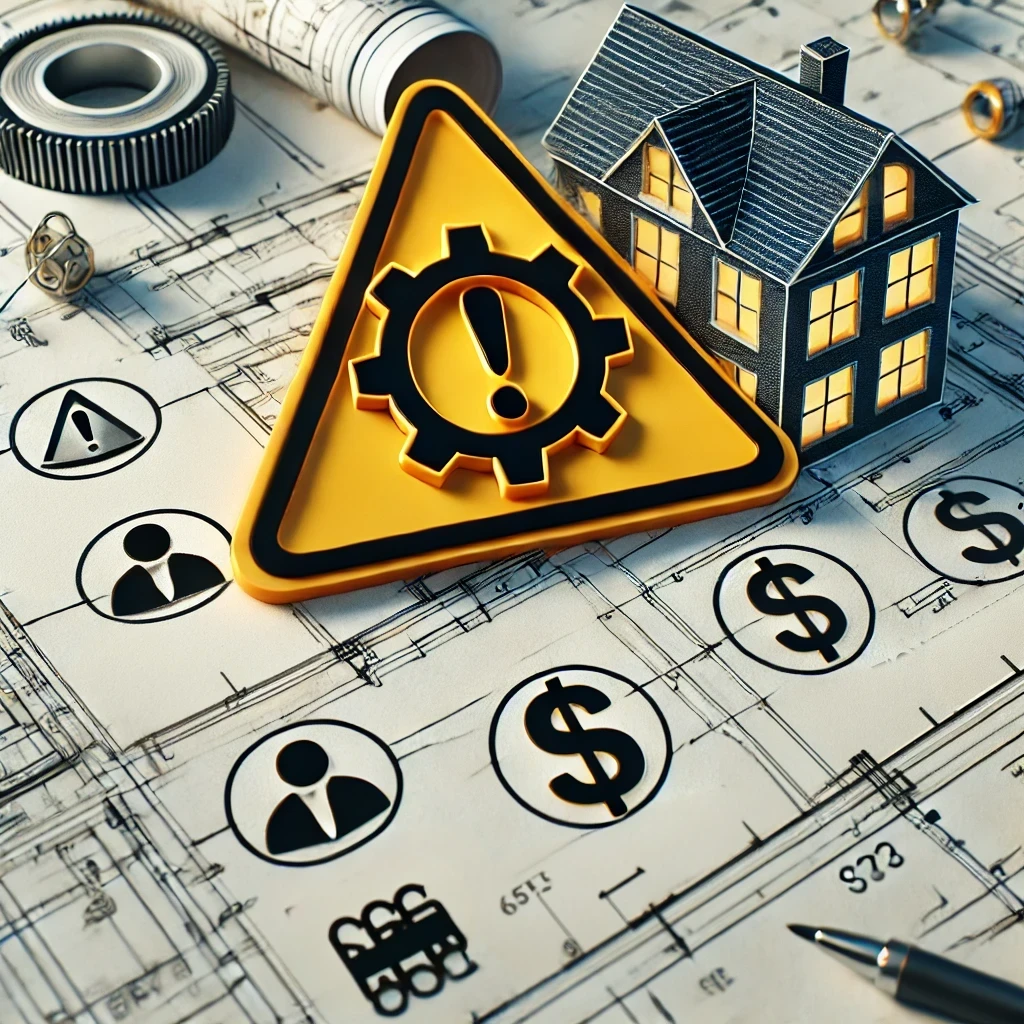
Mechanical, Electrical, and Plumbing (MEP) engineering plays a critical role in the functionality and safety of buildings. Given the complexity of these systems, MEP engineering projects are exposed to a range of risks, including design errors, system failures, regulatory non-compliance, and cost overruns. Mitigating these risks through effective planning is essential to ensure smooth operations, safety, and cost control. This article explores strategies for mitigating risks in MEP engineering through thorough planning and strategic implementation.
Early Involvement of MEP Engineers in the Design Process
One of the most important strategies for risk mitigation in MEP engineering is to involve MEP engineers early in the design process. Collaborating with architects, structural engineers, and contractors from the project's onset ensures that MEP systems are integrated seamlessly into the building design, avoiding costly design changes later.
Key Benefits:
- Prevents Conflicts: Early coordination helps prevent conflicts between MEP systems and architectural or structural elements, such as improper duct placement or insufficient space for mechanical equipment.
- Improves System Efficiency: Early input from MEP engineers allows the design to incorporate energy-efficient HVAC, electrical, and plumbing systems tailored to the building’s specific needs.
- Cost Savings: Identifying potential design issues early helps prevent costly redesigns and construction delays.
Thorough Risk Assessment and Identification
Effective risk management starts with a comprehensive risk assessment. By identifying potential risks early in the project, MEP engineers can develop mitigation strategies tailored to each risk type, reducing the likelihood of problems during construction or operation.
Steps for Risk Assessment:
- Identify Common Risks: Consider common risks such as system failures, code non-compliance, coordination issues, and unexpected costs.
- Analyze the Impact: Evaluate how each risk could affect the project in terms of safety, cost, and schedule.
- Prioritize Risks: Focus on high-impact risks that could cause significant disruptions, such as improper electrical load balancing or plumbing failures.
Building Information Modeling (BIM) for Coordination and Risk Reduction
Utilizing Building Information Modeling (BIM) technology is a highly effective way to mitigate risks in MEP engineering. BIM allows for the creation of a detailed, 3D digital representation of the building’s MEP systems, making it easier to coordinate various components and detect issues early.
Benefits of BIM in Risk Mitigation:
- Clash Detection: BIM helps identify potential clashes between MEP systems and other building elements (e.g., ductwork conflicting with structural beams), reducing rework and delays.
- Improved Communication: A shared BIM model fosters better communication between stakeholders, reducing misunderstandings and improving collaboration between the design and construction teams.
- Data-Driven Decision Making: BIM allows engineers to analyze the system's performance virtually, optimizing the design before actual installation and minimizing the risk of design flaws.
Code Compliance and Regulatory Adherence
Compliance with local, state, and national building codes is critical to avoiding legal risks and ensuring the safety and functionality of MEP systems. Early planning should include a detailed review of relevant codes and standards to ensure that all aspects of the MEP design are compliant.
Key Practices for Code Compliance:
- Stay Updated on Codes: MEP engineers must stay current on changes in building codes and industry standards, such as those set by ASHRAE, NEC (National Electrical Code), and IPC (International Plumbing Code).
- Incorporate Safety Standards: Ensure that designs meet fire safety, ventilation, and energy efficiency standards to reduce risks related to non-compliance.
- Engage with Code Consultants: Involving code consultants early in the planning process helps ensure that the design complies with all necessary regulations, minimizing the risk of delays or rework.
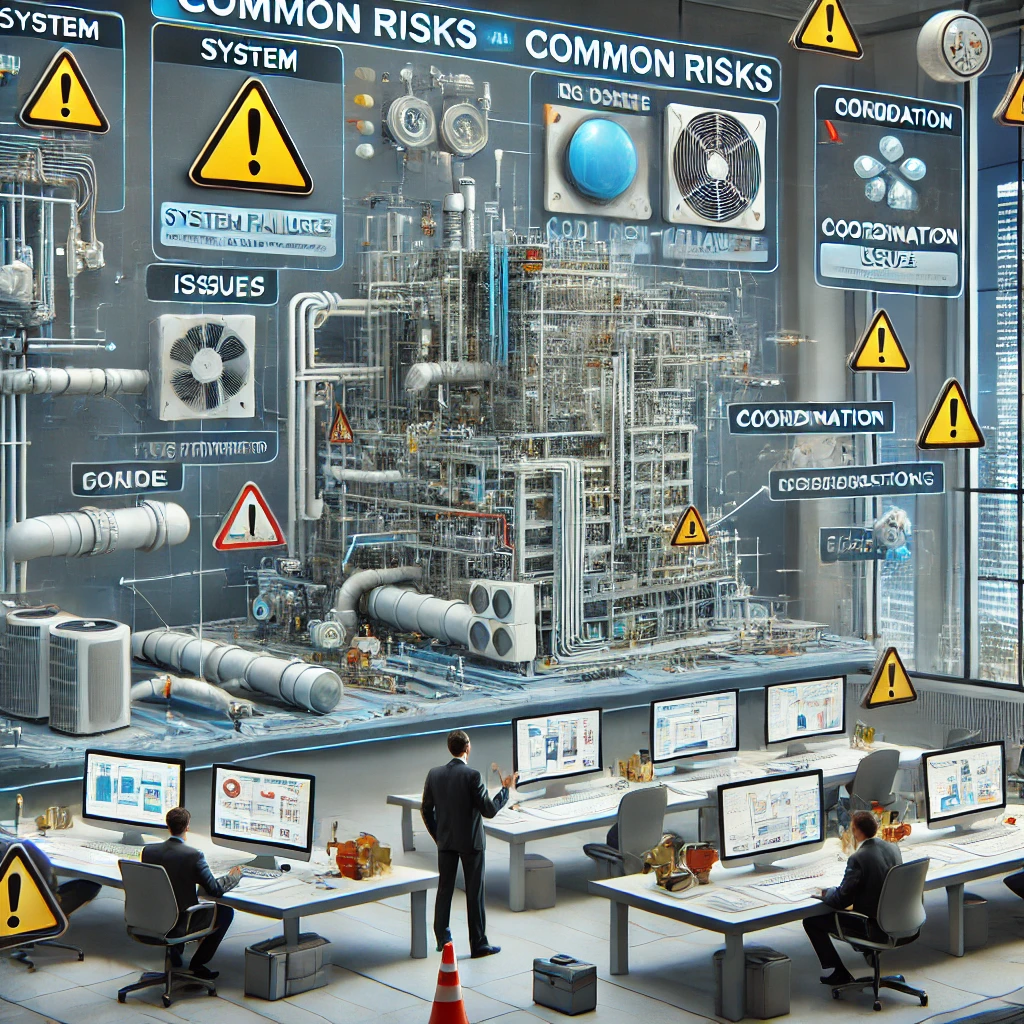
Value Engineering for Cost Control
Managing costs is a significant challenge in MEP engineering projects. Value engineering, a method that involves optimizing systems to reduce costs without compromising functionality, helps mitigate the risk of budget overruns.
Strategies for Value Engineering:
- Optimize System Efficiency: Choose energy-efficient equipment that may have higher upfront costs but offers long-term savings through reduced energy consumption and maintenance.
- Standardization: Use standardized components where possible to reduce procurement costs and improve installation efficiency.
- Focus on Lifecycle Costs: Evaluate systems based on their total lifecycle costs, including maintenance, energy use, and replacement expenses, to ensure long-term cost-effectiveness.
Contingency Planning for Unexpected Issues
Even with thorough planning, unforeseen issues can arise during construction or operation. Developing contingency plans allows MEP teams to respond quickly and effectively to these issues, reducing their potential impact on the project.
Elements of a Strong Contingency Plan:
- Budget Reserves: Set aside a portion of the project’s budget as a contingency fund to cover unexpected costs, such as equipment delays or system redesigns.
- Schedule Flexibility: Build flexibility into the construction schedule to accommodate potential delays, ensuring the project stays on track even if issues arise.
- Risk Monitoring: Continuously monitor project progress and potential risks, adjusting the contingency plan as needed to respond to emerging challenges.
Quality Control and Testing
WEnsuring the quality of MEP systems through regular inspections and testing is vital for minimizing the risk of system failures. Implementing a rigorous quality control plan reduces the likelihood of defects or malfunctions, ensuring that systems function as designed.
Best Practices for Quality Control:
- Pre-installation Inspections: Inspect equipment and materials before installation to ensure they meet the project’s specifications and quality standards.
- System Testing: Test HVAC, electrical, and plumbing systems after installation to verify their performance and compliance with design requirements.
- Ongoing Monitoring: Implement ongoing maintenance and monitoring systems that track system performance and detect potential issues early, preventing costly breakdowns.
Communication and Collaboration Across Teams
Effective planning requires strong communication and collaboration between all stakeholders, including MEP engineers, architects, contractors, and building owners. Clear communication ensures that everyone is on the same page, reducing the risk of errors, misinterpretations, or delays.
Key Strategies for Effective Communication:
- Regular Coordination Meetings: Hold regular meetings with all stakeholders to discuss project progress, identify potential risks, and develop solutions collaboratively.
- Clear Documentation: Provide clear and detailed documentation of MEP designs, including specifications, code compliance reports, and testing results, to ensure everyone understands the project’s requirements.
- Integrated Project Management Tools: Use project management software to track progress, share updates, and facilitate communication between teams in real-time.
Conclusion
Effective planning is critical to mitigating risks in MEP engineering projects. By involving MEP engineers early in the design process, conducting thorough risk assessments, using BIM technology, ensuring code compliance, and implementing quality control measures, project teams can reduce the likelihood of system failures, cost overruns, and delays. Strong communication and collaboration between all stakeholders further enhance the project's success, leading to safer, more efficient buildings with fewer long-term issues.
Category: