Best Practices for MEP Design in Complex Architectural Projects
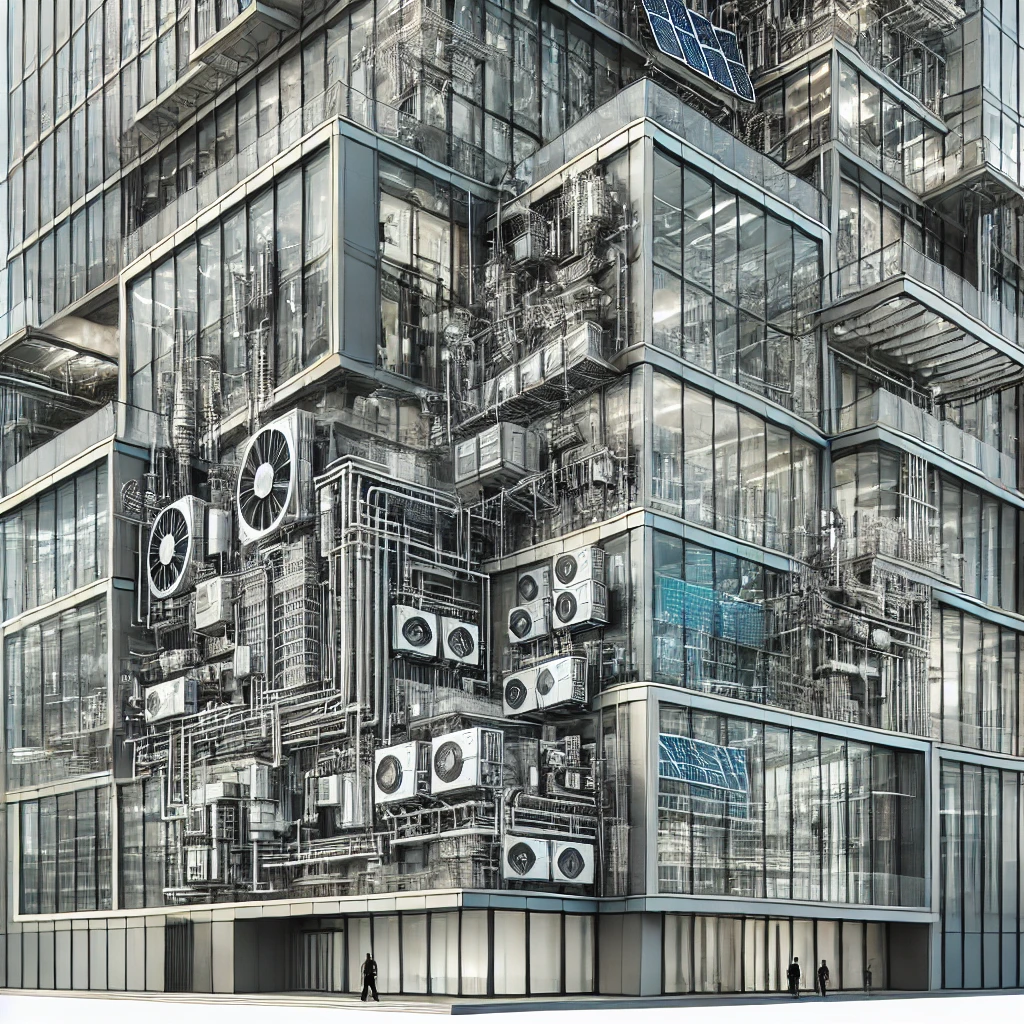
Mechanical, Electrical, and Plumbing (MEP) systems are critical to the functionality, comfort, and sustainability of any building, especially in complex architectural projects. These projects often present unique challenges that require careful planning and design. Effective MEP design ensures that systems work efficiently, meet regulatory standards, and integrate seamlessly with the architecture. Here are the best practices for successful MEP design in such settings.
Early Integration of MEP in the Design Process
One of the key best practices is involving MEP engineers early in the design phase of a project. Early collaboration between architects, structural engineers, and MEP specialists can prevent costly redesigns later. By integrating MEP systems from the beginning, the design team ensures that the building’s layout accommodates these systems without compromising aesthetics or functionality.
Best Practices:
- Optimize space utilization for mechanical rooms, ductwork, and electrical systems.
- Prevent conflicts between architectural elements and MEP systems.
- Enhance energy efficiency by designing systems suited to the building’s layout and climate.
BIM (Building Information Modeling) for Coordination
Using BIM technology is a best practice that significantly improves MEP coordination in complex architectural projects. BIM allows for the creation of a 3D model that integrates architectural, structural, and MEP components into one cohesive system. This collaborative approach helps identify and resolve clashes between systems before construction begins.
Best Practices:
- Provide a clear visualization of how MEP systems interact with the building’s design.
- Reduce errors and rework during the construction phase.
- Facilitate better communication between teams through a shared model.
Focus on Energy Efficiency and Sustainability
Incorporating sustainable design principles is crucial for modern MEP design, especially as more projects aim for LEED certification or other green building standards. Systems such as energy-efficient HVAC, renewable energy sources like solar panels, and advanced water management systems help reduce the building’s environmental impact.
Best Practices:
- Design HVAC systems with variable refrigerant flow (VRF) and demand-controlled ventilation to optimize energy use.
- Integrate renewable energy sources where possible, such as solar power or geothermal energy.
- Use energy modeling tools to assess and improve building performance early in the design phase.
Adaptability and Future-Proofing
Complex projects often serve multiple purposes over their lifespan, which means MEP systems need to be adaptable. Designing flexible systems that allow for future upgrades, expansions, or technological advancements can add significant value to the project.
Best Practices:
- Use modular and scalable MEP systems, especially in electrical and HVAC designs.
- Design systems with room for additional capacity for future needs.
- Incorporate smart building technologies that enable monitoring and remote management of systems
Space Planning and Efficiency
Maximizing space efficiency while accommodating MEP systems is a challenging but essential part of complex architectural projects. Properly planned mechanical rooms, vertical shafts for ductwork, and cable trays for electrical systems ensure smooth integration without taking up valuable floor space.
Best Practices:
- Work closely with the architectural team to find optimal locations for MEP equipment.
- Use compact, high-efficiency mechanical equipment when space is limited.
- Design efficient ductwork and piping layouts to minimize space consumption.
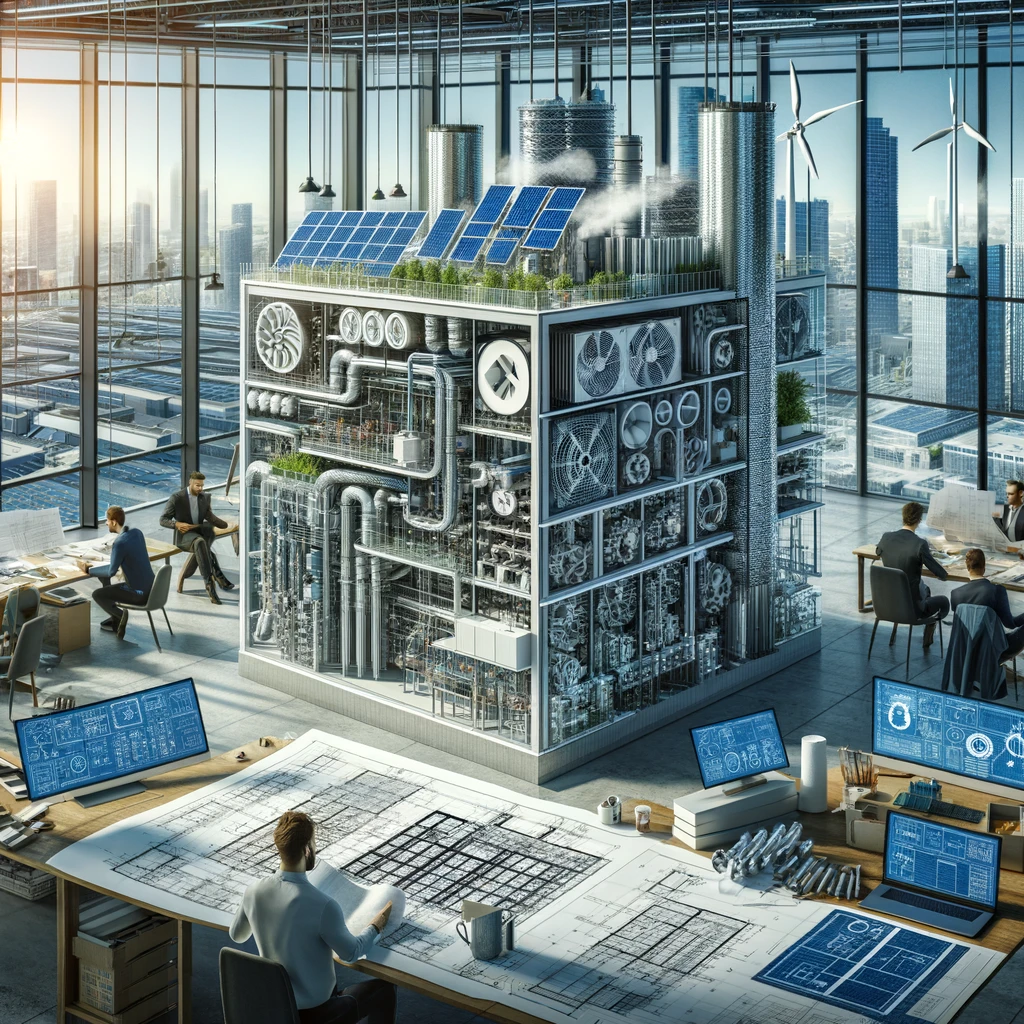
Compliance with Codes and Regulations
Navigating local, state, and national building codes is an integral part of MEP design. Ensuring compliance with all applicable codes prevents legal issues and costly modifications later in the project. This includes fire safety codes, electrical standards, and plumbing requirements.
Best Practices:
- Stay updated on relevant building codes and ensure designs meet all requirements.
- Engage with code consultants or local authorities early in the design phase.
- Use compliant materials and system components to meet regulatory standards.
Noise and Vibration Control
In complex architectural projects, especially those involving commercial or residential spaces, controlling noise and vibrations from MEP systems is critical to occupant comfort. Proper insulation and soundproofing techniques can significantly reduce noise from HVAC systems, plumbing, and electrical components.
Best Practices:
- Isolate mechanical equipment with vibration dampers and mounts.
- Design ductwork and piping with sound attenuation in mind.
- Use quiet-running fans and pumps to minimize operational noise.
Lifecycle Cost Analysis
Rather than focusing solely on initial costs, conducting a lifecycle cost analysis (LCCA) can ensure the MEP systems are cost-effective over the long term. This practice evaluates not only installation costs but also operational expenses, maintenance, and energy consumption over the building’s life.
Best Practices:
- Help in selecting energy-efficient systems that reduce long-term operating costs.
- Provide a clearer picture of return on investment (ROI) for high-performance MEP systems.
- Support decision-making for selecting materials and equipment with lower maintenance needs.
Collaboration and Communication Across Teams
A successful MEP design is built on strong collaboration and communication across all teams involved in the project. Regular coordination meetings, clear documentation, and open communication channels between MEP engineers, architects, contractors, and other stakeholders are essential for minimizing misunderstandings and ensuring smooth project execution.
Best Practices:
- Schedule regular coordination meetings with all design and construction teams.
- Maintain clear documentation and revisions of MEP designs.
- Use project management tools to track progress and communication.
Testing and Commissioning
Before a project is handed over, thorough testing and commissioning of MEP systems ensure that everything functions as intended. This process involves testing HVAC systems, electrical circuits, plumbing, and fire safety systems to verify their performance and compliance with design specifications.
Best Practices:
- Pre-commissioning checks for individual systems.
- Full system commissioning to ensure all components operate efficiently.
- Ongoing monitoring to address any post-installation issues.
Conclusion
MEP design in complex architectural projects requires a combination of technical expertise, early collaboration, and a forward-thinking approach. By following these best practices, project teams can ensure that MEP systems are efficient, sustainable, and seamlessly integrated into the overall architectural design, delivering buildings that meet performance and occupant needs for years to come.
Category: